The continuous carbonization furnace is a kind of high-efficiency and energy-saving carbonization equipment which can make wooden materials like wood sawdust or peanut shell into charcoal. This equipment can continuously carbonize for 24 hours, realizing simultaneous feeding and discharging. During the carbonization process, the materials will produce combustible gases such as carbon monoxide, methane, and hydrogen. After passing through the flue gas purification system, the combustible gas can undergo secondary combustion to achieve the effect of reciprocating heating and carbonization. The recycling of combustible gas not only saves energy but also avoids the problem of environmental pollution. The continuous carbonization furnace is the ideal equipment for the mass production of charcoal.
The structure of the rotary charcoal carbonzation furnace
The whole set of equipment is mainly composed of the gasifier, carbonization furnace, flue gas purification device, conveying device, etc.
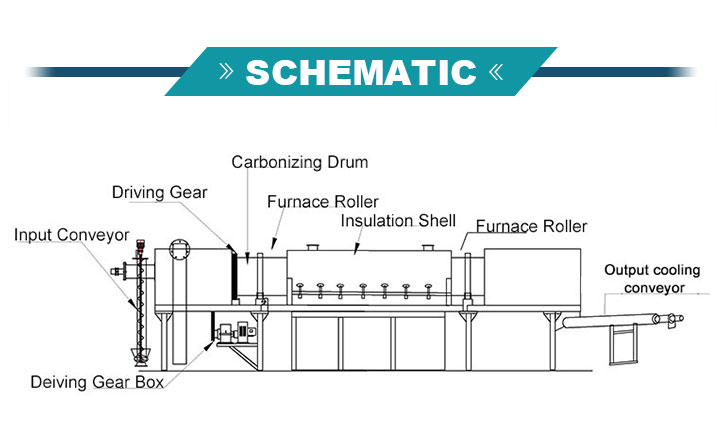
In the early stage, the gasification furnace is used to heat up the carbonization furnace. After a period of preheating, the material enters the carbonization furnace through the screw conveyor and begins to be carbonized under the rotation of the furnace body. The raw materials will produce a series of combustible flue gas during the carbonization process. The flue gas is sprayed, cooled, purified, and separated after being recovered, and then sent to the combustion chamber by the induced draft fan to continuously heat the carbonization furnace. At this time, the heating of the gasifier can be gradually turned off, and only the flue gas generated during the carbonization process is used for heating. The finished product after carbonization is finally input into the silo after cooling the discharging machine.
Working Principle of Rotary charcoal carbonization furnace
The carbonization process of materials in the carbonization furnace is mainly divided into the drying stage, the initial stage of carbonization, the full carbonization stage, and the cooling stage.
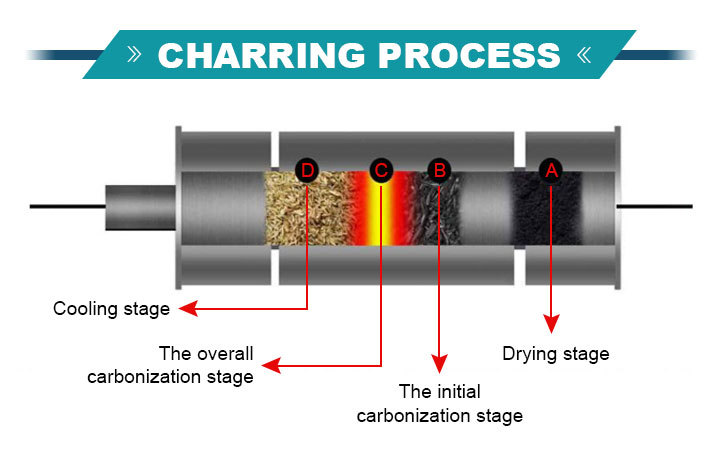
- Drying stage: From the ignition and heating of the gasification furnace, the temperature in the furnace rises to a certain temperature. At this time, the moisture contained in the material mainly relies on the heat generated by external combustion to evaporate, and the chemical composition of the material does not change much at this time.
- The initial stage of carbonization: This stage mainly relies on the combustion of the material itself to generate heat and raise the temperature in the furnace to the temperature required for carbonization. At this time, the material undergoes thermal decomposition reaction and its chemical composition has changed. Some unstable components decompose slowly.
- Full carbonization stage: In this stage, the wood material undergoes a rapid thermal decomposition reaction, and a large amount of liquid products such as acetic acid, methanol and wood tar are generated at the same time. In addition, flammable gases such as methane and ethylene are produced, and these flammable gases are burned in the furnace. The thermal decomposition reaction and gas combustion generate a lot of heat, which increases the temperature in the furnace, and the wood material is dry distilled into charcoal at high temperature.
- Cooling stage: After the material is carbonized, it needs to be cooled before storage, otherwise it is flammable in air.
The materials of the charcoal carbonization furnace
Continuous carbonization furnace is mainly used for materials with biomass properties such as sawdust, peanut husks, corn stalks, branches, rice husks, etc.
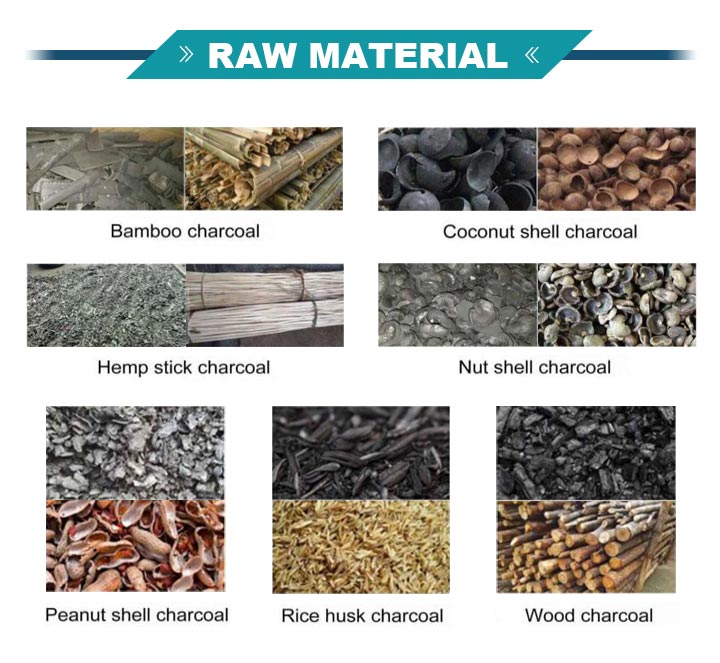
The advantage of the continuous carbonization furnace
- Rotary carbonization furnace has the advantage of high degree of automation, which can realize continuous operation for 24 hours.
- The flue gas recovery, incineration and dust removal devices ensure that the flue gas meets the emission standards.
- Coil cooling and water cooling augers ensure rapid cooling of materials, and have the advantages of smaller floor space and space saving compared with similar equipment.
- The whole set of equipment adopts bucket elevator to save time and effort.
- For some sawdust with a small particle size, it is easy to pile up in the ordinary carbonization furnace, resulting in incomplete thermal carbonization. And our rotary carbonization furnace guarantees the perfect carbonization effect.
- The drum-type continuous carbonization furnace has uniform heating, fast heat transfer and uniform carbonization. On average, it can carbonize 3-5 tons of materials per hour, which is 10-20 times the production efficiency of a static carbonization furnace.
Technical parameter for Rotary charcoal carbonization furnace
Type | SL-1200 |
Dimension(m) | 11.5*2*1.9m |
Capacity(kg/h) | 2000kg/h |
Total Power(kw) | 25 |
Input size | Less than 10cm |
Carbonization ratio for coconut shells | 3:1(3 t coconut shells:1t charcoal) |
Carbonization Temperature(℃) | 600-800 |
The display of the continuous carbonization furnace
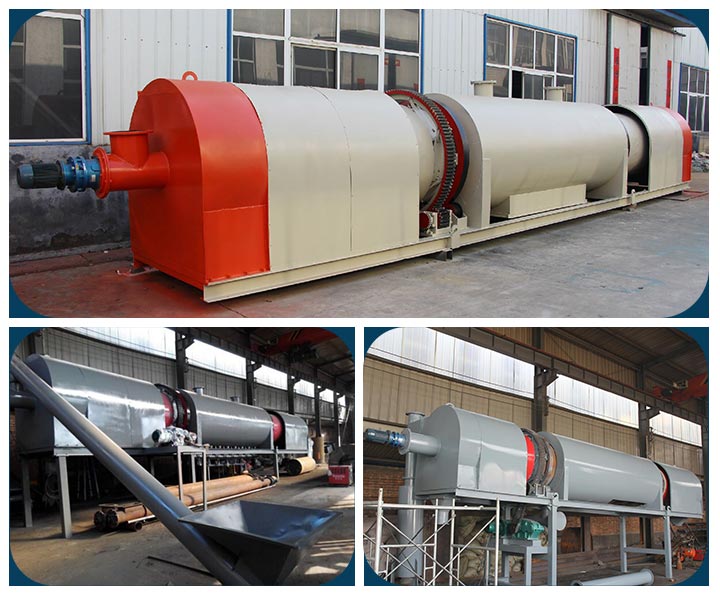