Im Arbeitsprozess der Sägemehl-Holzkohle-Maschinenflussausrüstung müssen wir die Betriebstechnologie der Ausrüstung beherrschen, um qualifizierte Brikettkohle herzustellen. Der Schlüssel zum Betrieb liegt in der Kontrolle der Temperatur bei der Herstellung von Holzkohle. Die aktuelle Montagelinie für Holzkohlemaschinen ist mit Temperaturkontrollmessgeräten und anderem Zubehör ausgestattet. Wir müssen die Temperaturanforderungen jedes Schritts verstehen, da die für die Rohstoffe in jedem Schritt erforderliche Temperatur nicht die gleiche ist. Und je nach Temperaturproduktion variiert auch die Herstellung von Holzkohle außerhalb des Briketts. Im Folgenden besprechen wir die Temperaturanforderungen jeder Phase des Produktionsprozesses der Brikettiermaschine, damit Sie diese während des Betriebs besser kontrollieren können.
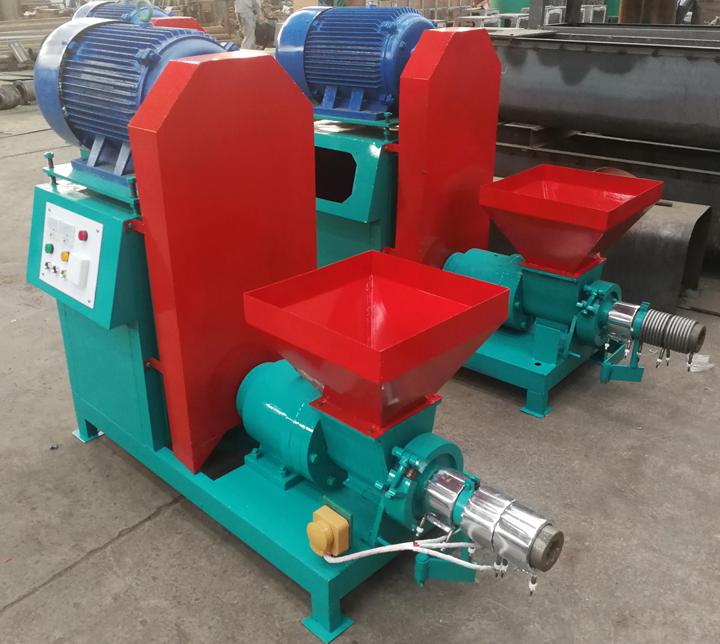
Die Bedeutung des Heizrings der Holzkohlebrikettmaschine
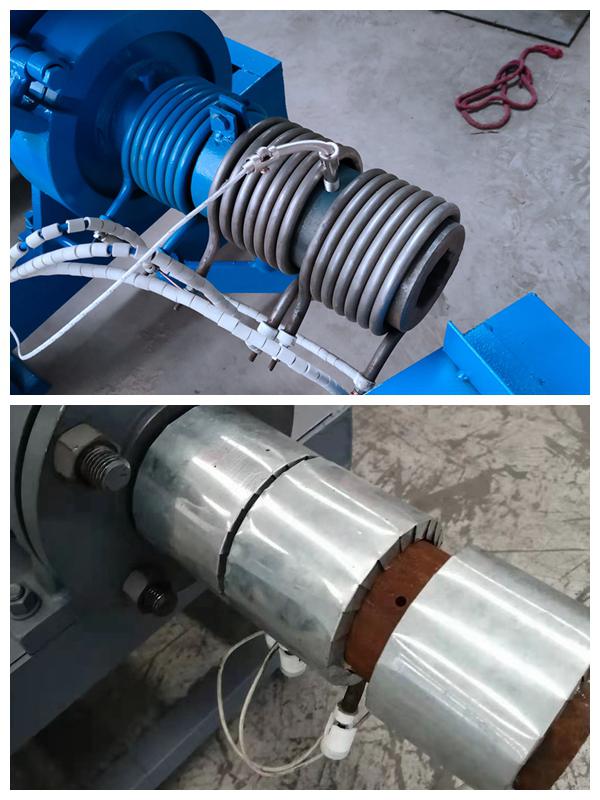
Der Heizring ist eines der wichtigeren Zubehörteile der Holzkohlebrikettmaschine und seine Funktion sollte nicht unterschätzt werden. Der Heizring ist an der Außenseite der Hülse angebracht und dient als Heizgerät, das die Holzspäne erhitzt. Die Holzspäne werden durch die hohe Temperatur und den hohen Druck des Heizrings geformt.
Das Funktionsprinzip der Heizspirale besteht darin, mithilfe eines Widerstandsdrahts Wärme zu erzeugen, mit geringem Stromverbrauch und einer Zeitspanne, in der die Wärmeenergie konzentriert wird. Das Außenmaterial des Halterings ist Edelstahl und die Innenseite ist ein hochohmiger Widerstand. Der Widerstand eines Heizrings beträgt 2 kW, wodurch sofort Wärme erzeugt und eine hohe Temperatur erreicht werden kann.
Ein Satz kleiner Holzkohlemaschinen ist mit drei Heizringen ausgestattet. Die Leistung des Heizrings bestimmt die Geschwindigkeit des Brikettiervorgangs. Derzeit werden üblicherweise drei Gruppen von 6-kW-Heizringen verwendet. Bei höherer Leistung verringert sich die Lebensdauer der Heizspirale, bei geringerer Leistung können Geschwindigkeit und Effizienz des Stabes nicht mithalten.
Die Temperaturanforderungen in jeder Phase des Brikettierprozesses
1. Trocknungsphase der Rohstoffe: Beim Trocknen der Rohstoffe können wir die Rohstoffe mit höherem Feuchtigkeitsgehalt 1 bis 2 Tage lang im Freilufttrocknungshof lagern, damit die Oberflächenfeuchtigkeit verdunsten kann, um die Trocknungszeit und den Kraftstoffverbrauch zu reduzieren. Verbrauch. Anschließend geben wir die Rohstoffe mit der geeigneten Partikelgröße in den Heißlufttrockner und trocknen sie, um Rohstoffe mit einem Feuchtigkeitsgehalt von weniger als 10% zu trocknen. Die Trocknungstemperatur beträgt im Allgemeinen etwa 140 ℃ bis 300 ℃.
2. Die Formungsphase der Rohstoffe: In der Maschine wird der Brikettierungsprozess der Rohstoffe abgeschlossen. Außerhalb der Formhülse der Brikettiermaschine befindet sich ein Heizring, der die Temperatur der Formhülse auf etwa 350 °C erhöhen kann. Um sicherzustellen, dass die Oberfläche der Brikettkohle glatt, dicht und rissfrei ist, können wir je nach Rohstoffart und Feuchtigkeitsgehalt die passende Formtemperatur wählen. Seine Höhe kann erst nach dem Feldversuch ermittelt werden. Im Allgemeinen gehen wir davon aus, dass der Schraubenpropeller geeignet ist und der Feuchtigkeitsgehalt des Rohmaterials zwischen 6 und 101 TP3T liegt. Die Trocknungstemperatur variiert je nach Materialform und Heizgerätmodell und liegt im Allgemeinen zwischen 140 und 500 °C ℃; Temperatur: Die Länge der Trocknungsleitung und die Verteilung des Luftvolumens können angepasst werden, um die Temperatur des Materials zu steuern und im Allgemeinen 5℃~7℃ nicht zu überschreiten.
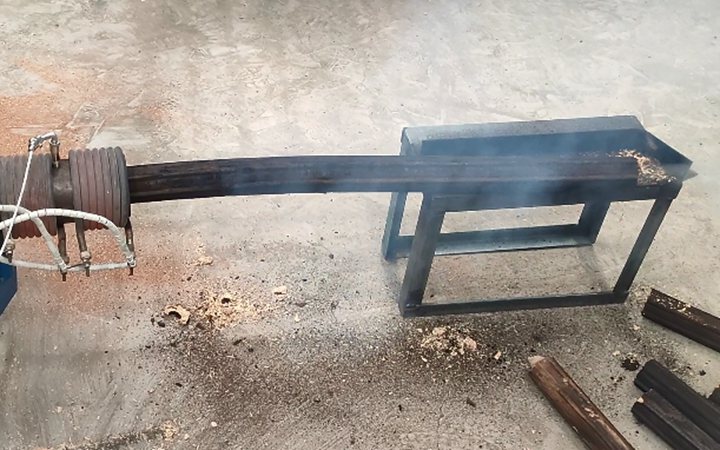
3. Die Karbonisierungsstufe der Rohstoffe: Von der Zündung an erhitzt der Verkokungsofen die Brennstäbe allmählich, bis die Ofentemperatur 160 Grad erreicht. Zu diesem Zeitpunkt verdunstet die in den Brennstäben enthaltene Feuchtigkeit, die chemische Zusammensetzung der Brennstäbe ändert sich jedoch nicht. , Der zweite Schritt der Karbonisierung beginnt allmählich. Zu diesem Zeitpunkt ist die Ofentemperatur von 160 Grad auf 280 Grad gestiegen. Bei dieser Temperatur handelt es sich im Allgemeinen um die Wärme, die vom eigenen Brennstoff des Brennstabs erzeugt wird. Das Holz beginnt sich zu verändern. Wenn die Temperatur auf 300 bis 650 Grad ansteigt, beginnen die Holzkohlestäbe weggeworfen und zersetzt zu werden, und die Holzkohle wird bei hoher Temperatur zu Holzkohle. In diesen drei Phasen müssen wir die Temperatur kontrollieren, um Verbrennungen und andere Phänomene zu verhindern. Wenn Sie es weiter auf Temperaturen zwischen 800 °C und 1000 °C erhitzen, wird die Graphitstruktur im Kohlenstoff zunehmen und auch die Leitfähigkeit nimmt zu. Zu diesem Zeitpunkt handelt es sich bei den hergestellten Kohlenstoffstäben um hochwertige Kohlenstoffstäbe.