Dans le processus de travail de l'équipement de flow de machine à charbon de sciure, nous devons maîtriser la technologie de fonctionnement de l'équipement pour produire du charbon de briquette de qualité. La clé de l'opération est de contrôler la température lors de la fabrication du charbon. L'équipement de ligne d'assemblage de machine à charbon actuel est équipé de compteurs de contrôle de température et d'autres accessoires, nous devons comprendre les exigences de température de chaque étape car la température requise pour les matières premières à chaque étape n'est pas la même. Et une production à des températures différentes, la fabrication de charbon de briquette variera également. Ci-dessous, nous allons parler des exigences de température de chaque étape du processus de production de la machine à briquettes afin que vous puissiez mieux le contrôler lors de l'opération.
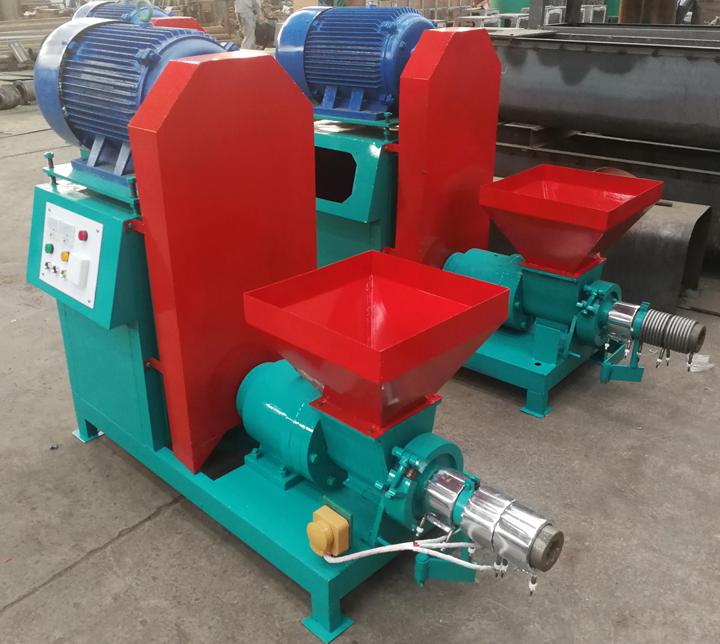
L'importance de l'anneau de chauffage de la machine à briquettes de charbon
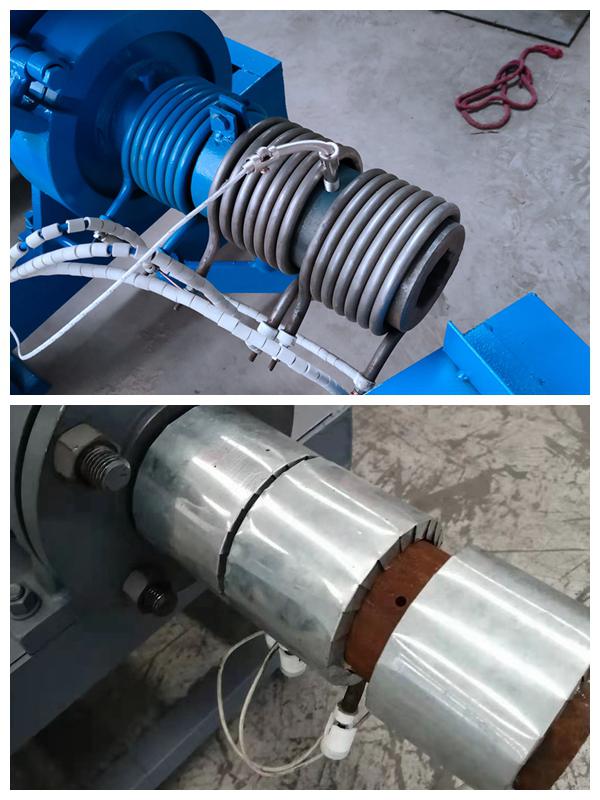
L'anneau de chauffage est l'un des accessoires les plus importants de la machine à briquettes de charbon, et sa fonction ne doit pas être sous-estimée. L'anneau de chauffage est installé à l'extérieur de la manchon, et sa fonction est un dispositif de chauffage qui chauffe les copeaux de bois, et les copeaux de bois sont formés par la haute température et la haute pression de l'anneau de chauffage.
Le principe de fonctionnement de la bobine de chauffage est d'utiliser un fil résistif pour générer de la chaleur, avec une faible consommation d'énergie et une période pendant laquelle l'énergie thermique est concentrée. Le matériau extérieur de l'anneau de maintien est en acier inoxydable, et l'intérieur est un résistor à haute résistance. La résistance d'un anneau de chauffage est de 2KW, ce qui peut générer de la chaleur instantanément et atteindre une température élevée.
Un ensemble de petits équipements de machine à charbon est équipé de trois anneaux de chauffage. La puissance de l'anneau de chauffage détermine la vitesse du processus de briquetage. Actuellement, trois groupes d'anneaux de chauffage de 6KW sont couramment utilisés. Si la puissance est plus élevée, la durée de vie de la bobine de chauffage sera réduite, et si la puissance est plus faible, la vitesse et l'efficacité de la tige ne suivront pas.
Les exigences de température à chaque étape du processus de briquetage
1. Étape de séchage des matières premières : Lors du séchage des matières premières, nous pouvons placer les matières premières avec une teneur en humidité plus élevée dans la cour de séchage à l'air libre pendant 1 à 2 jours pour laisser l'humidité de surface s'évaporer afin de réduire le temps de séchage et la consommation de combustible. Ensuite, nous plaçons les matières premières avec une taille de particule qualifiée dans le séchoir à air chaud et les séchons jusqu'à obtenir des matières premières avec une teneur en humidité inférieure à 10 %. La température de séchage est généralement d'environ 140 ℃ à 300 ℃.
2. L'étape de formation des matières premières : Le processus de briquetage des matières premières est terminé dans la machine. Il y a un anneau chauffant à l'extérieur de la manche de formation de la machine à briquettes, qui peut augmenter la température de la manche de formation à environ 350°C. Afin de garantir que la surface du charbon de briquette soit lisse, dense et sans fissures, nous pouvons choisir la température de moulage appropriée en fonction du type de matière première et de la teneur en humidité. Sa hauteur ne peut être déterminée qu'après le test sur le terrain. En général, nous supposons que la vis propulseur est qualifiée, et que la teneur en humidité de la matière première est comprise entre 6 et 10 %, et que la température de séchage : varie selon la forme du matériau et le modèle du chauffage, généralement entre 140 ℃ et 500 ℃ ; Température : La longueur du pipeline de séchage et la distribution du volume d'air peuvent être ajustées pour contrôler la température du matériau, généralement ne dépassant pas 5℃~7℃.
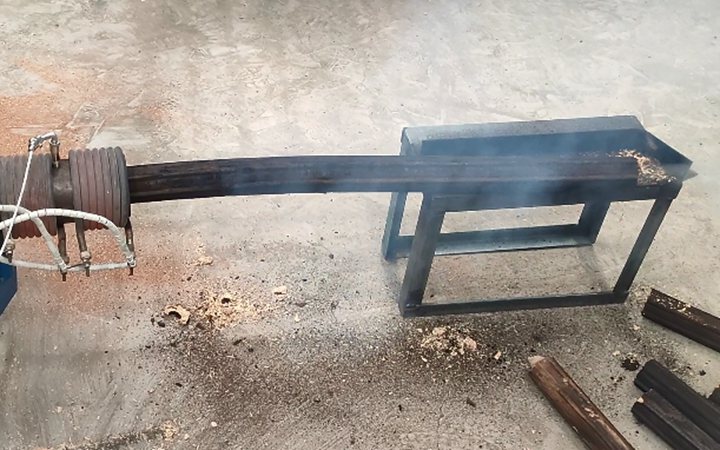
3. L'étape de carbonisation des matières premières : Depuis l'allumage, le four de carbonisation chauffe progressivement les barres de combustible jusqu'à ce que la température du four atteigne 160 degrés. À ce moment-là, l'humidité contenue dans les barres de combustible s'évapore, mais la composition chimique des barres de combustible ne change pas. La deuxième étape de la carbonisation est sur le point de commencer progressivement. À ce moment-là, la température du four est passée de 160 degrés à 280. Cette température est généralement la chaleur générée par le combustible des barres de combustible elles-mêmes. Le bois commence à changer. Lorsque la température atteint 300 degrés et jusqu'à 650 degrés, les barres de charbon commencent à être rejetées et décomposées, et le charbon devient charbon à haute température. Dans ces trois étapes, nous devons contrôler la température pour éviter les brûlures et d'autres phénomènes. Si vous continuez à chauffer jusqu'à ce que la température soit comprise entre 800 °C et 1000 °C, la structure de graphite dans le carbone augmentera, et la conductivité augmentera également. À ce moment-là, les barres de carbone produites sont des barres de carbone de haute qualité.