In seeking sustainable and eco-friendly energy solutions, coconut shell charcoal has become a notable choice. Made from the vast quantities of coconut shells thrown away annually, this natural biofuel presents a practical alternative to conventional fuels like firewood and kerosene. Here’s a step-by-step guide on creating coconut shell charcoal, from gathering the raw materials to producing the final product.
Why make coconut shell charcoal?
Coconut shell charcoal offers numerous benefits, making it a better option than traditional charcoal.
- Renewable resource: its production helps prevent deforestation.
- Low ash residue: the ash generated can be utilized as fertilizer.
- Longer burning time: it burns hotter and lasts longer, meaning you need less charcoal for barbecues.
- Clean burning: it produces very little smoke and pollutants.
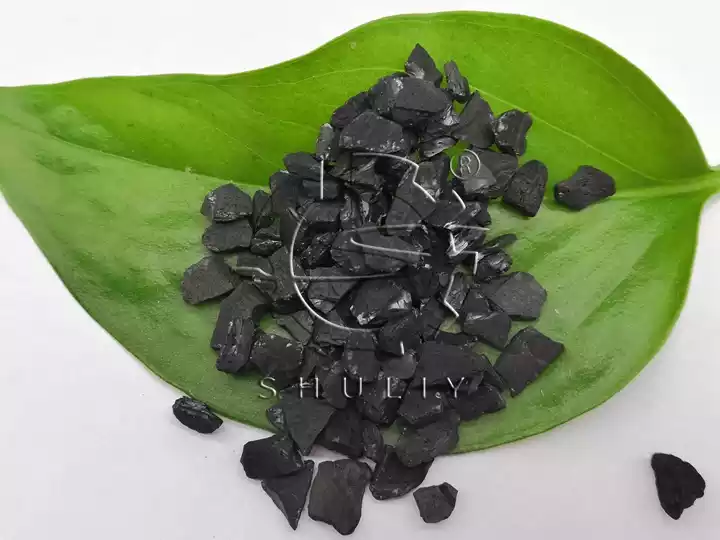
Sourcing coconut shells
Coconut shells are a plentiful resource found in tropical regions where coconuts are abundant. Typically thrown away after coconut milk is extracted, these shells can be easily obtained at low cost from roadside collections, markets, and coconut processing facilities. This readily available and affordable material serves as the foundation for producing coconut shell charcoal.
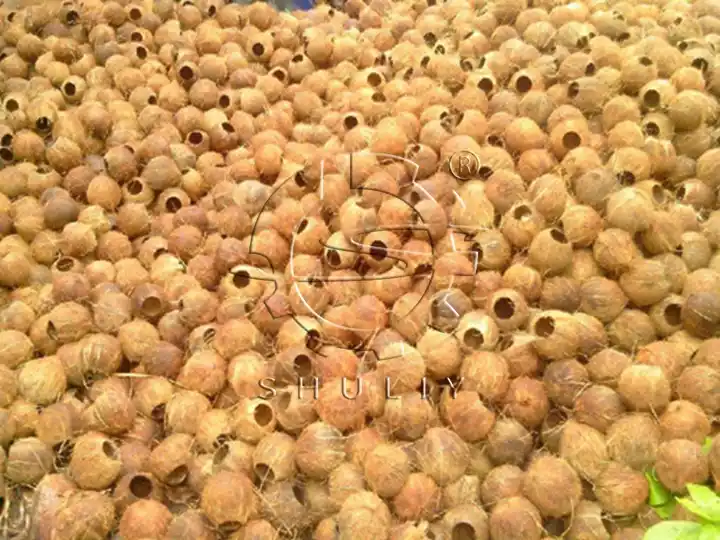
Preparing the factory setup
Before starting the production process, there are a few essential factors to consider.
- Raw materials: a consistent supply of coconut shells is necessary.
- Power supply: three-phase industrial electricity is crucial for the machine’s operation.
- Other requirements: access to water, a suitable workshop, and available labor.
For more detailed planning and tailored solutions, feel free to reach out to us directly. We offer comprehensive guidance based on your unique needs and requirements.
The whole process of coconut shell charcoal
The following lists the steps in sequence for making coconut shell coal briquettes.
Carbonization process
This process transforms coconut shells into charcoal using controlled heat treatment. We provide a variety of carbonization furnaces to meet different production needs, whether small or large scale.
For small-scale production, hoisting-type carbonization furnaces and horizontal airflow carbonizers are perfect. For large-scale production, continuous charcoal charring furnaces deliver both efficiency and scalability.
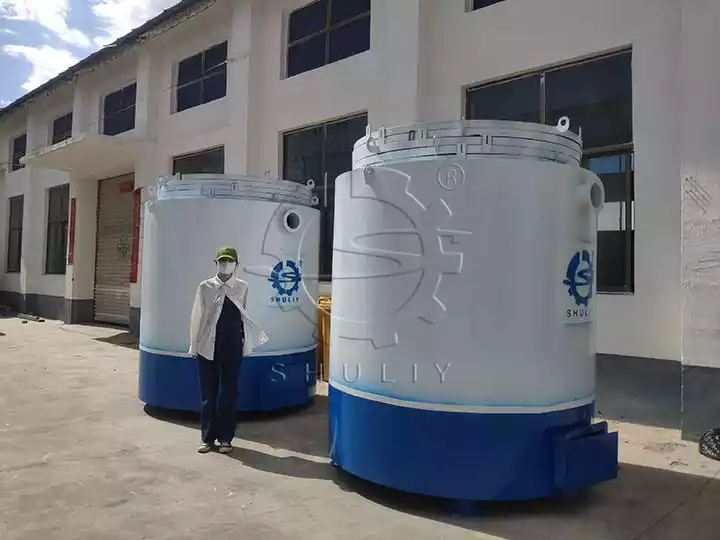
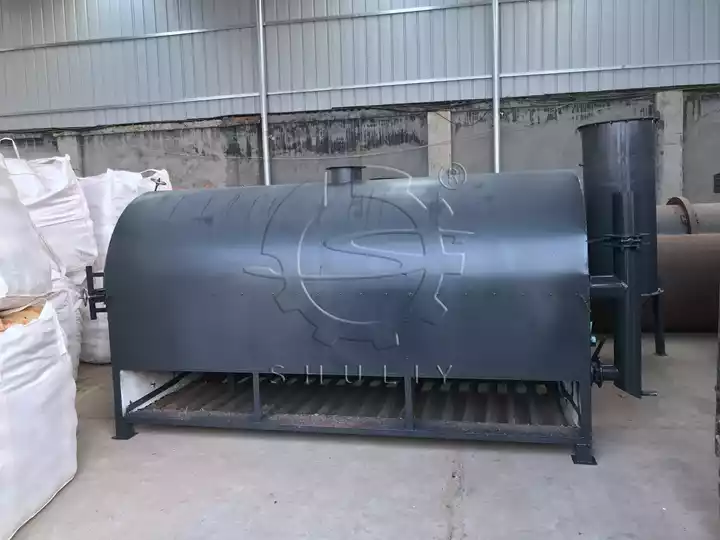
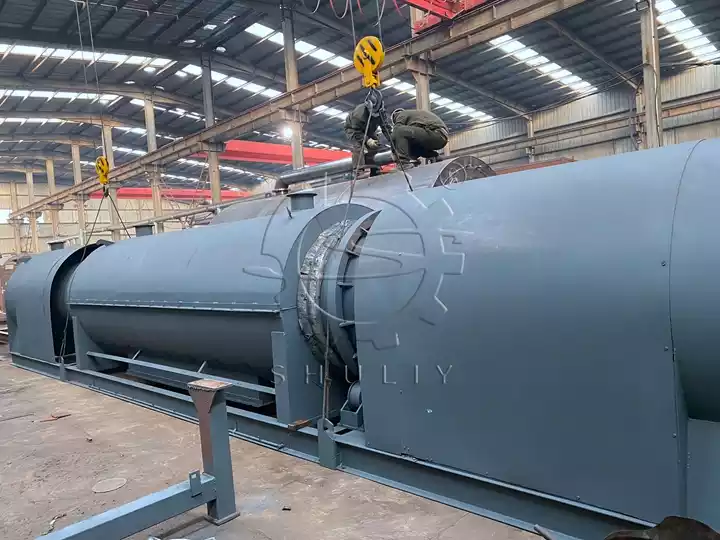
Crushing and mixing
After carbonization, coir charcoal may keep its shell shape or break into smaller pieces. To make further processing easier, these fragments should be crushed into a fine powder. This not only aids in molding but also minimizes wear and tear on the machinery.
Charcoal powder is not sticky, so binders need to be added to create agglomerates. Typically, the binder content ranges from 3-5%, and the mixture should maintain a moisture level of 20-25%. A simple way to test the moisture content is to take a handful of the mixture; if it holds together without crumbling, it has the right amount of moisture.
Forming the mixture into briquettes
Once the mixture is prepared, the next step involves forming it into agglomerates with the help of specialized machines. Various machines create agglomerates in different shapes and sizes, each tailored for specific uses, with the most common being charcoal briquettes extruder machines, hookah charcoal machines, and charcoal ball press machines.
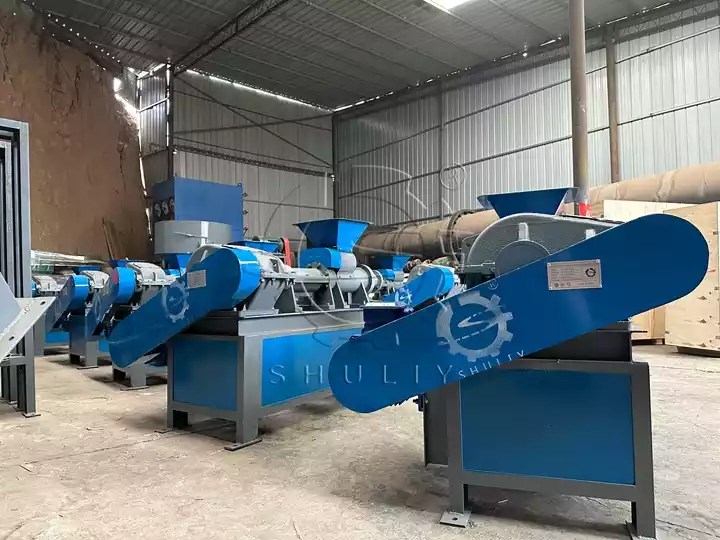
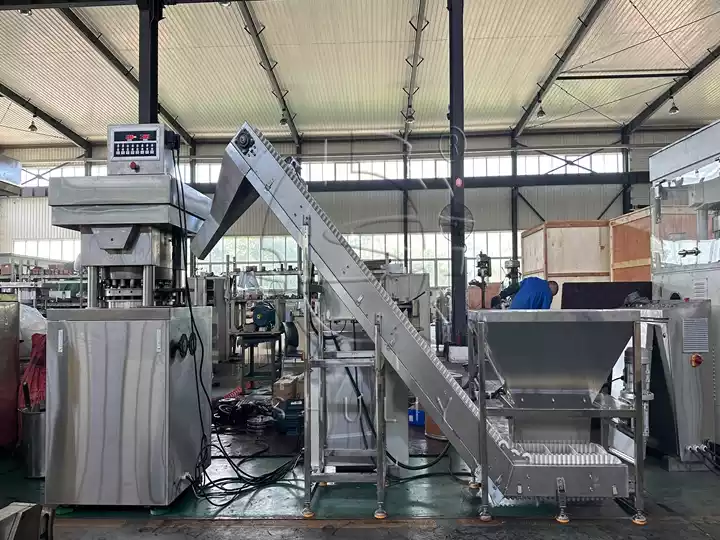
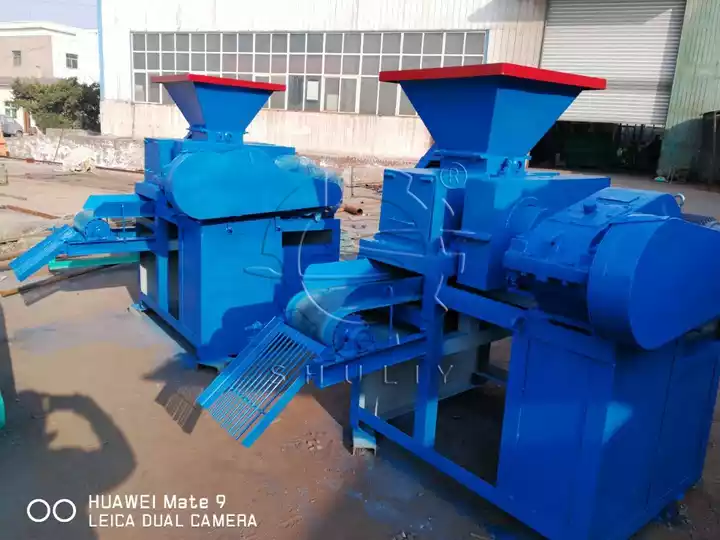
Drying
Freshly produced charcoal briquettes are damp and must be dried before they can be used or sold. There are two common drying methods:
- Natural drying: the briquettes are laid out on pallets or plastic sheets and left to dry in the sun. This process typically takes 4-7 days and requires protection from rain and contaminants.
- Machine drying: this method employs a mesh belt dryer or a box dryer. Mesh belt dryers provide fully automated operation and can complete the drying in just 2-3 hours. In contrast, box dryers take around 5 hours and can be powered by either combustion or electricity.
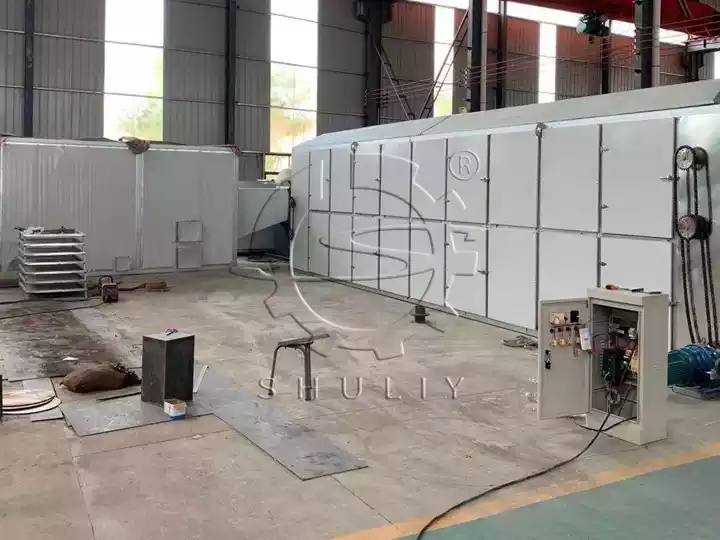
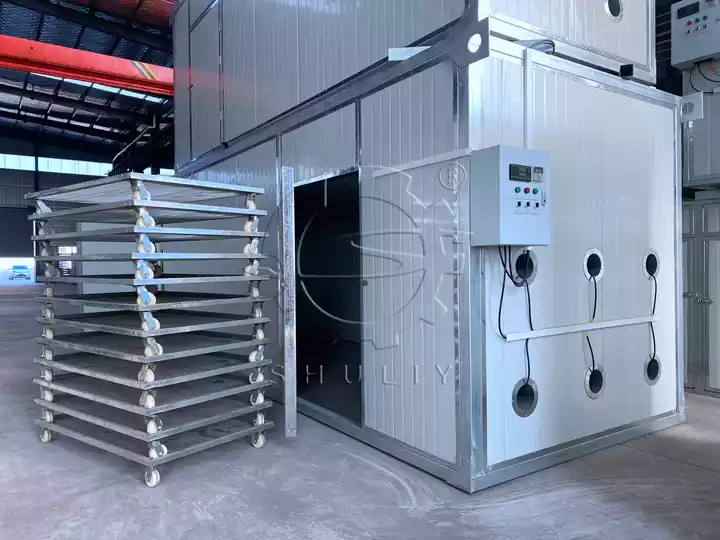
In short, making coconut shell charcoal is a sustainable and profitable business. Please feel free to contact us for the latest costs and solutions for coconut shell charcoal production!