Kadar arang peralatan briket serbuk gergaji juga merupakan indikator penting keluaran peralatan briket serbuk gergaji. Itu mesin briket serbuk gergaji memiliki hasil karbon yang tinggi dan output yang tinggi. Namun dalam proses produksi sebenarnya selalu ada beberapa faktor yang mempengaruhi laju arang pada mesin briket serbuk gergaji. Oleh karena itu sebelum menggunakan peralatan mesin briket serbuk gergaji perlu dipahami faktor-faktor apa saja yang mempengaruhi laju arang pada mesin briket serbuk gergaji tersebut.
Kadar arang pada mesin briket serbuk gergaji menunjukkan perbedaan tertentu karena jenis bahan bakunya berbeda. Meskipun suhu karbonisasi yang lebih rendah dapat memperoleh laju penghilangan karbon yang lebih tinggi, namun arang yang dihasilkan memiliki kualitas dan sifat korosif yang rendah serta mengandung zat tar yang bersifat asam, sehingga tidak dapat dibakar sebagai nyala api bersih tanpa asap.
Karbon komersial berkualitas tinggi harus memiliki kandungan karbon padat lebih dari 80%, yang memerlukan suhu karbonisasi akhir dikontrol di atas 500 °C. Kandungan serat kayu pada bahan baku berpengaruh positif terhadap rendemen arang.
Peralatan briket serbuk gergaji menghasilkan bahan yang lebih matang dan strukturnya lebih kokoh. Dengan meningkatnya suhu karbonisasi maka kerapuhan arang juga akan meningkat. Dalam produksi aktual, ditemukan bahwa ketika suhu karbonisasi akhir antara 550 ° C dan 650 ° C, kerapuhan arang dan kandungan karbon padat dapat mencapai keseimbangan yang lebih baik.
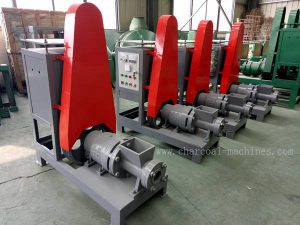
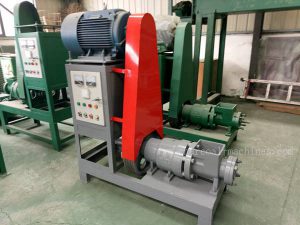
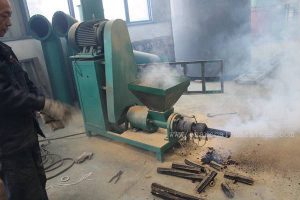
Mesin briket serbuk gergaji terutama digunakan untuk memproduksi peralatan arang. Mesin tersebut dapat memanfaatkan bahan limbah untuk menghasilkan arang, yang tidak hanya memecahkan masalah penggunaan kembali bahan limbah, tetapi juga mengurangi tingginya permintaan arang di pasar. Pada kenyataannya penggunaan mesin briket serbuk gergaji, beberapa hasilnya rendah karena karbonisasi batang.
Serbuk gergaji yang dihasilkan oleh mesin briket serbuk gergaji memiliki hasil yang rendah, dan ada beberapa masalah yang disebabkan oleh masalah ini:
A. Posisi penyalaan yang tidak tepat: posisi penyalaan terlalu dekat dengan lubang suplai oksigen, sehingga timbul nyala api terbuka pada lubang suplai oksigen (pintu kiln), sehingga menyebabkan fenomena banyaknya arang di pintu kiln. Penyelesaian masalah ini terutama dengan memperbaiki posisi penyalaan sehingga posisi penyalaan mendekati bagian tengah kiln.
B. Proses pemanasan yang terlalu lama: terkadang hal ini disebabkan oleh petugas arang yang mengabaikan waktu penutupan kiln, sehingga menyebabkan waktu pemanasan menjadi terlalu lama dan membuang sebagian arang yang telah hangus.
C. Cerobong kiln tidak dapat diakses: cerobong asap tidak akan memperpanjang waktu karbonisasi, sehingga sebagian arang akan terbakar lebih banyak, sehingga cerobong asap dan cerobong harus dipastikan pada saat kiln dipasang.
d, kebocoran gas kiln: kebocoran gas kiln perlu diperbaiki tepat waktu.
e. Terlalu banyak oksigen dalam proses karbonisasi: Masalah ini lebih rumit. Personel arang harus terus-menerus mengamati suhu tanur dan mengatur pasokan oksigen.