Dalam proses kerja peralatan aliran mesin arang serbuk gergaji, kita harus menguasai teknologi pengoperasian peralatan tersebut agar dapat menghasilkan briket arang yang berkualitas. Kunci pengoperasiannya adalah mengontrol suhu saat membuat arang. Peralatan perakitan mesin arang yang ada saat ini sudah dilengkapi dengan pengatur suhu meter dan aksesoris lainnya, perlu kita pahami kebutuhan suhu pada setiap tahapan karena suhu yang dibutuhkan bahan baku pada setiap tahapan tidak sama. Dan berbeda suhu produksinya, produksi arang out-of-briket juga akan berbeda-beda. Di bawah ini kami akan membahas persyaratan suhu setiap tahap proses produksi mesin briket sehingga Anda dapat mengontrolnya dengan lebih baik selama pengoperasian.
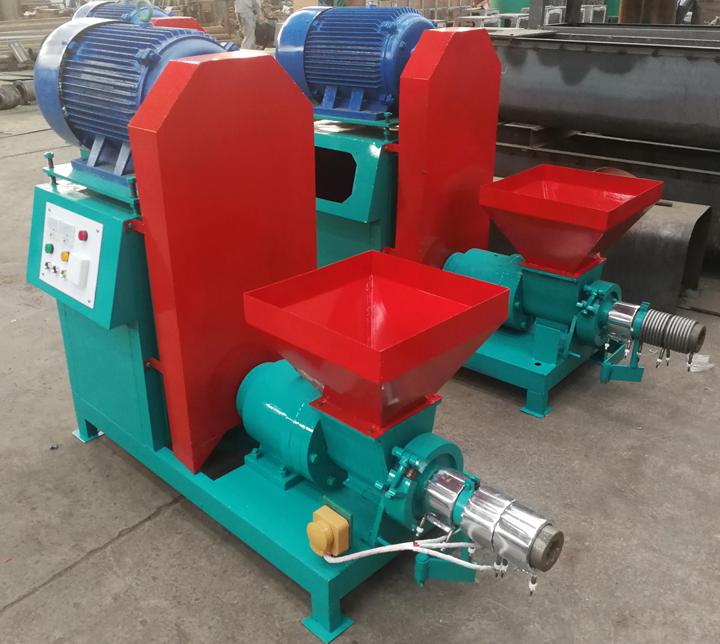
Pentingnya cincin pemanas mesin briket arang
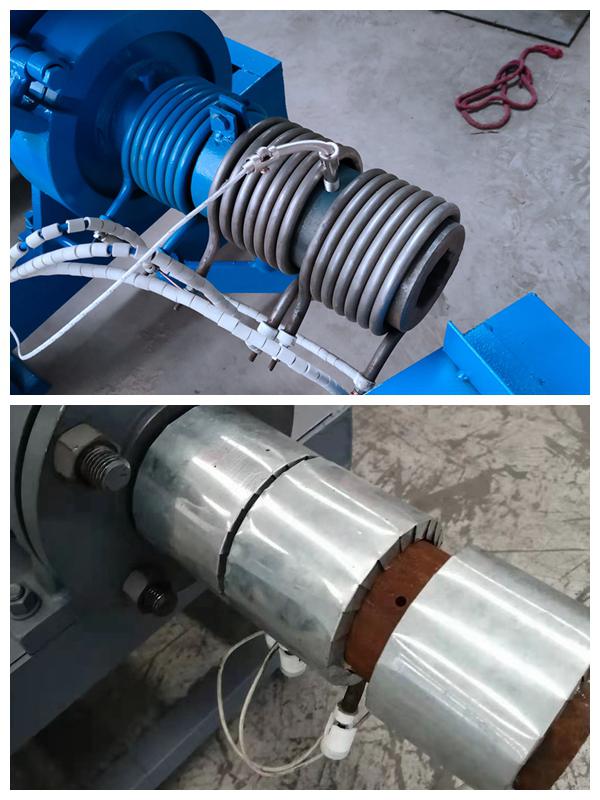
Cincin pemanas merupakan salah satu aksesoris penting pada mesin briket arang, dan fungsinya tidak boleh dianggap remeh. Cincin pemanas dipasang di bagian luar selongsong, dan fungsinya sebagai alat pemanas untuk memanaskan serpihan kayu, dan serpihan kayu tersebut terbentuk oleh suhu tinggi dan tekanan tinggi dari cincin pemanas.
Prinsip kerja koil pemanas adalah menggunakan kawat resistansi untuk menghasilkan panas, dengan konsumsi daya yang rendah dan jangka waktu ketika energi panas terkonsentrasi. Bahan luar cincin penahan adalah baja tahan karat, dan bagian dalamnya adalah resistor resistansi tinggi. Hambatan dari cincin pemanas adalah 2KW, yang dapat menghasilkan panas secara instan dan mencapai suhu tinggi.
Satu set peralatan mesin arang kecil dilengkapi dengan tiga cincin pemanas. Kekuatan cincin pemanas menentukan kecepatan proses pembuatan briket. Saat ini, tiga kelompok cincin pemanas 6KW yang umum digunakan. Jika daya lebih tinggi, masa pakai koil pemanas akan berkurang, dan jika daya lebih rendah, kecepatan dan efisiensi batang tidak akan bisa mengimbangi.
Persyaratan suhu pada setiap tahap proses pembuatan briket
1. Tahap pengeringan bahan baku: Saat mengeringkan bahan mentah, kita dapat meletakkan bahan mentah dengan kadar air lebih tinggi di tempat pengeringan terbuka selama 1 hingga 2 hari agar kelembapan permukaan menguap guna mengurangi waktu pengeringan dan konsumsi bahan bakar. Konsumsi. Kemudian bahan baku dengan ukuran partikel yang memenuhi syarat dimasukkan ke dalam pengering udara panas dan dikeringkan hingga bahan baku kering dengan kadar air kurang dari 10%. Suhu pengeringan umumnya sekitar 140 ℃ ~ 300 ℃.
2. Tahap pembentukan bahan baku: Proses pembuatan briket bahan baku selesai di dalam mesin. Terdapat cincin pemanas di luar selongsong pembentuk mesin briket, yang dapat meningkatkan suhu selongsong pembentuk hingga sekitar 350°C. Untuk memastikan permukaan arang briket halus, padat, dan bebas retak, kita dapat memilih suhu pencetakan yang sesuai dengan jenis bahan baku dan kadar air. Ketinggiannya hanya dapat ditentukan setelah uji lapangan. Secara umum, kami berasumsi bahwa baling-baling sekrup memenuhi syarat, dan kadar air bahan mentah antara 6-10%, dan suhu pengeringan: bervariasi sesuai dengan bentuk bahan dan model pemanas, umumnya antara 140 ℃ dan 500 ℃; Suhu: Panjang pipa pengeringan dan distribusi volume udara dapat diatur untuk mengontrol suhu material, umumnya tidak melebihi 5℃~7℃.
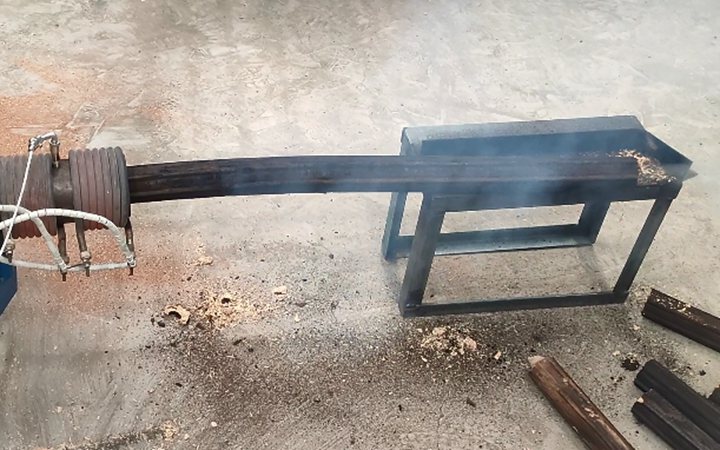
3. Tahap karbonisasi bahan baku: Dari penyalaan, tungku karbonisasi secara bertahap memanaskan batang bahan bakar hingga suhu tungku mencapai 160 derajat. Pada saat ini, uap air yang terkandung dalam batang bahan bakar akan menguap, namun komposisi kimia batang bahan bakar tidak akan berubah. , Langkah kedua karbonisasi akan dimulai secara bertahap. Saat ini suhu tungku telah meningkat dari 160 derajat menjadi 280. Suhu ini umumnya merupakan panas yang dihasilkan oleh bahan bakar batang bahan bakar itu sendiri. Kayu mulai berubah. Ketika suhu naik hingga 300 derajat hingga 650 derajat, batang arang mulai dibuang dan terurai, dan arang menjadi arang pada suhu tinggi. Dalam ketiga tahap ini, kita harus mengontrol suhu untuk mencegah pembakaran dan fenomena lainnya. Jika Anda terus memanaskannya hingga suhu antara 800°C dan 1000°C, struktur grafit dalam karbon akan meningkat, dan konduktivitasnya juga akan meningkat. Saat ini batang karbon yang dihasilkan merupakan batang karbon yang berkualitas tinggi.