톱밥 숯 기계 흐름 장비의 작업 과정에서 자격을 갖춘 연탄 숯을 생산하려면 장비의 작동 기술을 숙지해야 합니다. 작업의 핵심은 숯을 만들 때 온도를 조절하는 것입니다. 현재 숯 기계 조립 라인 장비에는 온도 조절 미터 및 기타 액세서리가 장착되어 있으며, 각 단계의 원료에 필요한 온도가 동일하지 않기 때문에 각 단계의 온도 요구 사항을 이해해야 합니다. 그리고 생산 온도가 다르면 연탄을 사용하지 않는 숯 제조도 달라집니다. 아래에서는 작동 중에 더 잘 제어할 수 있도록 연탄 기계 생산 공정의 각 단계의 온도 요구 사항에 대해 설명합니다.
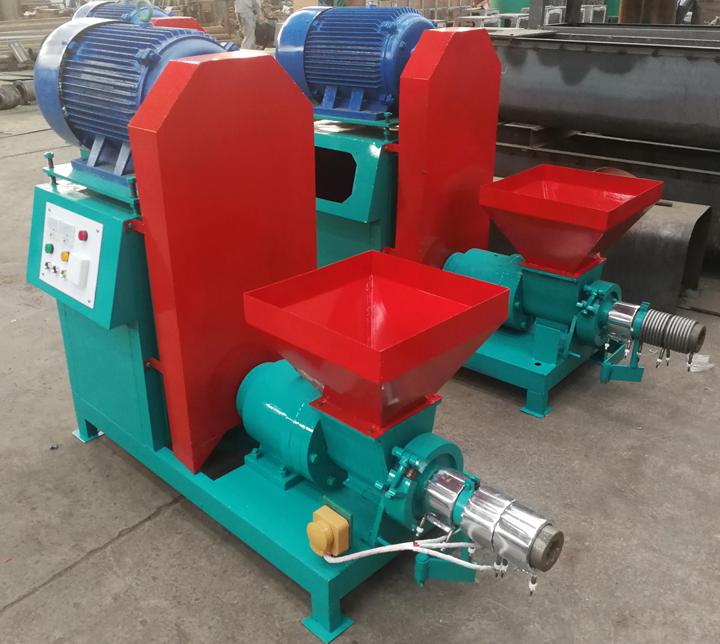
숯불 연탄 기계의 가열 링의 중요성
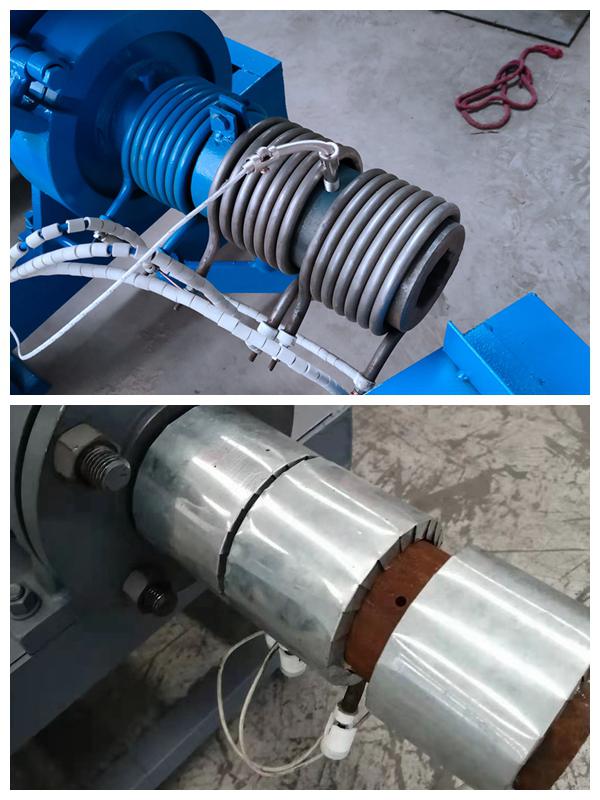
가열 링은 숯 연탄 기계의 가장 중요한 액세서리 중 하나이며 그 기능을 과소평가해서는 안 됩니다. 슬리브 외부에 히팅링이 설치되어 그 기능은 우드칩을 가열하는 가열장치이며, 히팅링의 고온, 고압에 의해 우드칩이 형성됩니다.
가열 코일의 작동 원리는 저항선을 사용하여 열을 발생시키고, 전력 소모가 낮으며, 열 에너지가 집중되는 시간을 갖는 것입니다. 고정 링의 외부 재질은 스테인레스 스틸이고 내부는 고저항 저항입니다. 가열 링의 저항은 2KW로 순간적으로 열을 발생시켜 고온에 도달할 수 있습니다.
작은 숯 기계 장비 세트에는 3개의 가열 링이 장착되어 있습니다. 가열 링의 힘은 연탄 공정의 속도를 결정합니다. 현재 6KW 가열 링의 세 그룹이 일반적으로 사용됩니다. 출력이 높으면 가열 코일의 수명이 줄어들고, 출력이 낮으면 로드의 속도와 효율이 따라가지 못합니다.
연탄 공정의 각 단계에서 요구되는 온도
1. 원료의 건조 단계: 원료를 건조할 때 수분 함량이 높은 원료를 야외 건조장에 1~2일 동안 넣어 표면의 수분을 증발시켜 건조 시간과 연료 소비를 줄일 수 있습니다. 소비. 그런 다음 적합한 입자 크기의 원료를 열풍 건조기에 넣고 건조하여 수분 함량이 10% 미만인 원료를 건조합니다. 건조온도는 일반적으로 140℃~300℃ 정도이다.
2. 원료의 형성 단계: 기계에서 원료의 연탄 공정이 완료됩니다. 연탄 기계의 성형 슬리브 외부에 가열 링이 있어 성형 슬리브의 온도를 약 350°C까지 높일 수 있습니다. 연탄탄의 표면이 매끄럽고 조밀하며 균열이 없도록 하기 위해 원료의 종류와 수분 함량에 따라 적절한 성형 온도를 선택할 수 있습니다. 높이는 현장 테스트 후에만 결정될 수 있습니다. 일반적으로 스크류 프로펠러는 자격을 갖추고 있으며 원료의 수분 함량은 6-10% 사이이고 건조 온도는 재료의 모양과 히터 모델에 따라 다르며 일반적으로 140 ℃에서 500 ℃ 사이라고 가정합니다. ℃; 온도: 건조 파이프라인의 길이와 공기량 분포를 조정하여 재료의 온도를 제어할 수 있으며 일반적으로 5℃~7℃를 초과하지 않습니다.
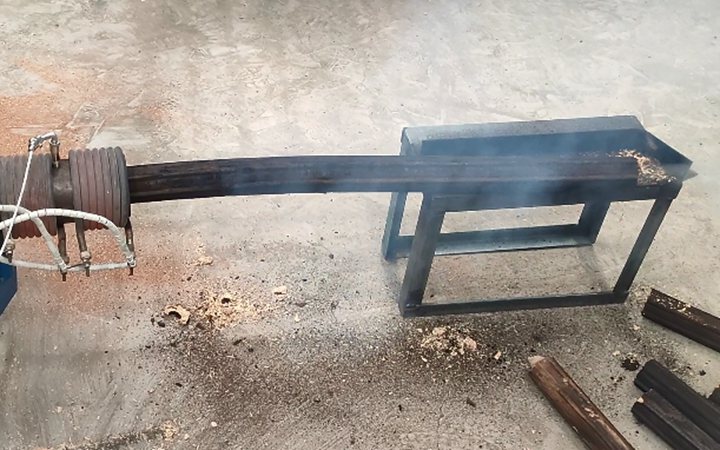
3. 원료의 탄화 단계: 착화부터 탄화로에서는 로 온도가 160도에 도달할 때까지 연료봉을 서서히 가열합니다. 이때 연료봉에 함유된 수분은 증발하지만 연료봉의 화학적 조성은 변하지 않습니다. , 탄화의 두 번째 단계가 점차 시작될 예정입니다. 이때 화로 온도는 160도에서 280도까지 올라갔다. 이 온도는 일반적으로 연료봉 자체 연료에서 발생하는 열이다. 나무가 변하기 시작합니다. 300도에서 650도까지 온도가 올라가면 숯봉이 버려지고 분해되기 시작하며, 높은 온도에서 숯이 숯이 됩니다. 이 세 단계에서는 타는 듯한 현상과 기타 현상을 방지하기 위해 온도를 조절해야 합니다. 계속 가열하면 온도가 800°C~1000°C가 될 때 탄소의 흑연 구조가 증가하고 전도성도 증가합니다. 이때 생산되는 탄소봉은 고품질의 탄소봉이다.